Why choose factory finish? Because it makes for a better looking and better performing finish. Having your cladding or decking pre finished or factory applied provides so many benefits. Pre finished wood cladding just looks better, but it also saves loads of time and money. When talking about exterior products this goes ten fold. Here are 7 reasons why you should get all of your decking, trim, and siding factory finished. The cost savings on pre finishing alone will shock you.
Save time & Space on the job site
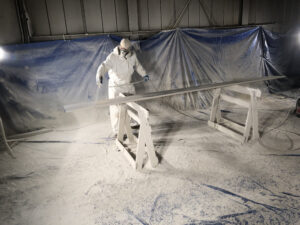
The most beneficial attribute of a factory-applied finish on natural wood is that it arrives ready to install. While this is a major advantage at any time of year, it is particularly helpful for projects in the cold winter months. Finishing on-site requires slightly warmer temperatures to make sure the finish cures properly. Most finish manufacturers will tell you that temperatures below 60 degree Fahrenheit will give you problems. They will also tell you not to finish in direct sunlight and to finish when there will be no rain for at least a few hours before and after applying. Oh – and don’t forget about the wind blowing dust around that settles into your curing finish, giving you that lovely “texture.”
Now let’s talk about space. You have that perfect window of weather opportunity, and you have to set up a herd of saw horses to lay out every board to brush, spray or roll on the finish. Oh – and don’t forget that any other work on the site that might create dust needs to stop while this finish is drying. Factory finishing removes these variables, as we are able to run all year long regardless of temperature, meaning you’ll be able to install right away.Â
No additional labor required on job site
Wood finishing is scary. The black magic of applying a finish and responding to different types of finish and different wood species is a job all by itself. This is why many woodworkers and carpenters have “a finishing guy” who they send their work to. So now you have a crew on site to specifically finish your material, while the rest of the crew has to stop working (see above). Finishing is a skill (an expensive one too), and by embracing a factory applied finish, you can skip that additional cost and line item on the day’s work schedule. Good help is hard to find. Even more difficult to find is knowledgeable and experienced finishers to do the work at the job site, because job site finishing is actually avoided by skilled finishers. So if the on-site work is done on different days by multiple people, differences in technique or application tools WILL create an inconsistent look. These differences make it difficult to estimate the amount of finish needed to complete the project. Not having enough finish can set your project back, especially if the job site is in a remote or difficult to reach area. But, also, finish applied poorly is not easily removed, so sometimes more wood itself may need to be ordered.
The best quality finishes and smoothest application
We have an entire building dedicated to finish application. Our equipment includes several machines designed to apply certain types of finishes with precision control to respond in real time when a natural material like wood absorbs finish differently. We have a crew of finish experts running these machines and making adjustments as the product is run. The consistency of a machine applied finish just can’t be beat by even the best finisher, but more importantly, having years of experience actively monitoring the machine gives you the best of both worlds. Moreover, with the volume of material which we finish, we have extensive knowledge of the products on the market as well as emerging technologies in coatings. I was joking earlier, but nano tech is a very real thing in the coatings world, and staying on top of these new products is essential. Just because we ran this varnish last year doesn’t mean it is the best option this year, and we constantly adapt with new products and new applications.
even finish on all sides
Consistency of application is important. Too thick a coat, and you can have appearance and drying issues. Too thin, and the same can be true. But, also, consistency of application on all the face of the wood is crucial. Whether oil or water based, finish introduces a lot of moisture to the wood which causes it to swell. If finish isn’t applied to all the face, or applied unevenly, then unpredictable movement will result. This can show up even weeks after the finish is dried, due to the inconsistent thickness of the coat applied. On a job site, finishing 4 sides of a board properly is essentially like putting on 4 coats of finish. In a factory setting, most machines can apply to all sides at once. Or if not possible, the coats applied are exactly the same thickness and mixture, so that even moisture absorption is happening from one side to the other and end to end.
Higher volume savings
Due to the volume of finishing we do, we are able to buy materials in larger quantities and pass that volume savings on to you. But more importantly, we maintain an inventory so that waiting on finishes to arrive are rarely a concern. All our materials are stored in climate controlled environments so they are ready to be applied. The colors and pigments we use are the highest quality but are also mixed precisely to ensure the color of gray used 6 months ago is the same shade being used today. You might be surprised how different the exact same finish will be buying off-the-shelf products years or even months apart.
Wood is just hard to finish
But let’s also look at the elephant in the room: wood. It’s an organic material. Each species is different, and even within a species one board to the next will be different and take finish differently. With the consistency provided by a controlled environment, precision machinery, and experts overseeing it all, we can pivot during a run to make sure that every board looks its best. Sometimes a job comes up and we know ahead of time which finish to use for that particular species and make recommendations to our customers to create a better performing product. This saves immensely down the road if a finish fails out in the field.
DRying & curing can break a wood finish
As stated above, the weather changes that can happen in the field can ruin a finish or cause it to fail before its time. Read the label on any can of finish, and you will see things like drying time and curing time. These can be drastically different numbers. They can also be changed substantially by the weather and prevent bonding and proper cross linking. Not only are we concerned about the proper application, but we are also concerned with how the finished wood is treated while it dries and cures. Our finishing room has plenty of drying racks to allow for even air flow around the entire board. But the real game changer is our drying room that speeds up not just the drying but also the cure time in a controlled manner. Also, going through the process at the factory means that any changes to the wood such as end checking or movement can be addressed before the wood is sent to you. This helps to eliminate any wonky boards and end the hassle of trimming on the job site completely.
The best Finish starts with finish Preparation
Most finishes need a little help binding to the surface of wood by sanding to give a little “tooth” to the wood. Lumber straight out of the mill will have what is known as mill glaze. High speed knives can burnish the wood with heat build up and hinder the absorption of a finish. Additionally, the knife marks left on the wood from even the best quality millwork will pop out clear as day once a finish is applied. So, to give the best looking finish but also the best absorption and adhesion of your finish, sanding is absolutely required. What can be a horrible job on site to hand sand every cladding or decking board can be accomplished quickly and extremely consistently at the mill with precision belt sanders set up inline with the finishing machines. Instead of dishing and swirl marks from hand sanding, you are presented with a flat and even surface that is thirsty and ready to absorb, resulting in more depth and luster to the wood and a more durable finish coat.
Shown below is the perfect example between an unsanded versus a sanded finished product. The same dyed oil-based finish was applied to both samples. On the left, you can see that the finish settled into the textured marks in the wood, but on the right, the sanded surface yields a perfectly smooth application, making the natural patterns in the wood pop.Â
Blend and Unify Color Differences
If you’ve worked with wood cladding or decking before, you’ll know of the natural variation you will find from board to board. Despite being the same wood species, boards will vary in color and grain pattern. This look can be undesirable, depending on the application. Most often, natural wood is chosen for this variation and the unique attributes that come with this choice. But some species will look better with a bit of color added in to the “clear” finish. This tiny bit of pigment can unify mineral staining and color variation brought on by a thousand natural variables as the trees grew. One such species is Cumaru, which can be found in red and yellow varieties that differ in appearance greatly, especially on a large scale project like a house or deck. This is where finishing comes in— as our decking finish options can solve this issue. A tinted oil-based finish on Cumaru still brings forth the natural look of the wood, while homogenizing the color, blending the yellow and red hues. The finish emphasizes the natural hues and ups the saturation, making a much more vibrant and homogenous final look. Not only does this finish blend the colors, but it also stabilizes and protects the wood from moisture. Applying a finish like this in a factory setting is the best way to ensure the smoothest application and best color blending results.
Pre Finished Wood Cladding Weathers More Gracefully
Your exterior woods will weather no matter how nano engineered, AI guided, and high tech your finish. You can choose to let it age to a silvery gray over time or refresh the finish every year or two. If that weathered look is your end goal, then you might be surprised that a pre finish is the better option. While it will slow the graying process, it will also make that process more uniform than unfinished wood. The pre finished wood cladding will age more evenly and gracefully with less of a patchy, awkward adolescence look due to the even coating and stabilization that modern coatings provide. Northern exposure wall, eaves and soffits, etc. will not get as much exposure and can maintain a fresh look longer than the high exposure areas. With a factory applied finish, all of the above elements of finish preparation, consistent application in climate controlled environments, and careful quality control will make for a much better weathering process. Consistent application equals consistent weathering of the wood – both 6 months down the road or 7 years later.
Pre finishing is actually cheaper
It’s clear that a factory finish is the best way to avoid the unpredictable nature of wood finishing. It is the very unpredictable nature that costs so much more. On the job site, if finishing goes poorly, there is very little recourse and extensive delays to fix it. Add on the additional time and labor and material costs, and your head will start to spin with all the things that can (and will) go wrong and cost you more money. It may be tough to think about adding more to your cost per square foot or linear foot when buying millwork. But even adding 40-60% on top of the material cost for factory finishing will ultimately save you a huge amount later – and this cost you can budget for. While we hope to incur no issues, a factory finished product that goes wrong can be addressed with us and fixed for you. However, if the finish goes wrong out in the field, we can’t help you fix it, and you certainly can’t get a credit on the material supplied. Yes, pre finishing costs more than raw wood. But the insurance provided in addition to the beauty of a well executed finish is priceless.
Looking to understand the additional costs and lead time you need to consider for your project? Get a quote today and let’s start a conversation about your project.
Leave a Reply